- 時間:2021-12-20
- 點擊:1383
- 來源:新甘肅
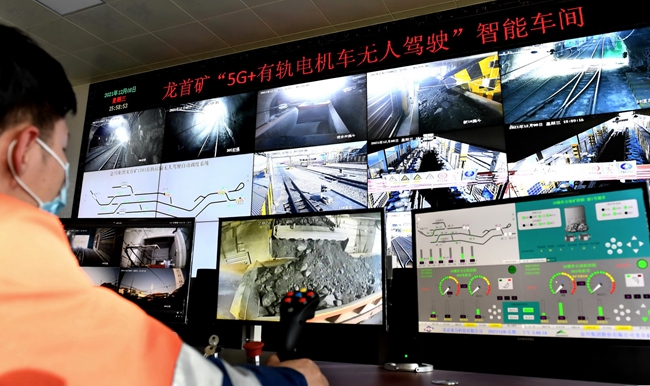
窗明幾凈的操作室里,職工靠操控手柄便完成礦車裝礦、轉(zhuǎn)換車頭、拉運、卸礦等一系列運輸工序。加上360度“無死角”大屏幕,生產(chǎn)現(xiàn)場全流程無人干預,這就是金川集團公司龍首礦“5G+有軌電車無人駕駛”智能化生產(chǎn)現(xiàn)場。
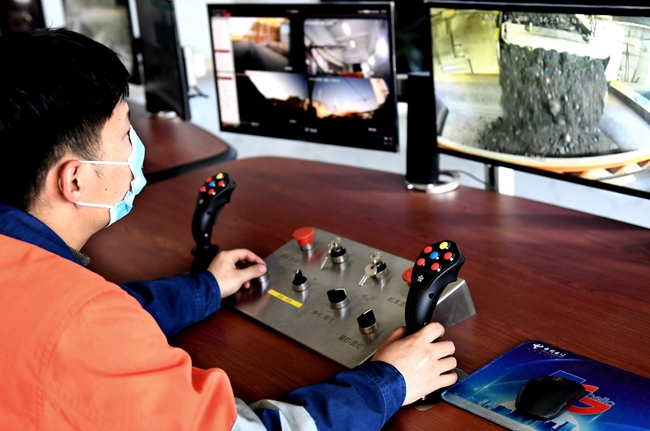
“以前我們電機車司機坐在駕駛室里,冬冷夏熱,噪音大,粉塵大,現(xiàn)在這些都成為歷史?!饼埵椎V智能車間操作員王斌介紹,傳統(tǒng)生產(chǎn)模式下,一趟礦車放礦、拉運、缷礦需要45分鐘左右,無人駕駛系統(tǒng)投用后,整個流程只需約30分鐘。
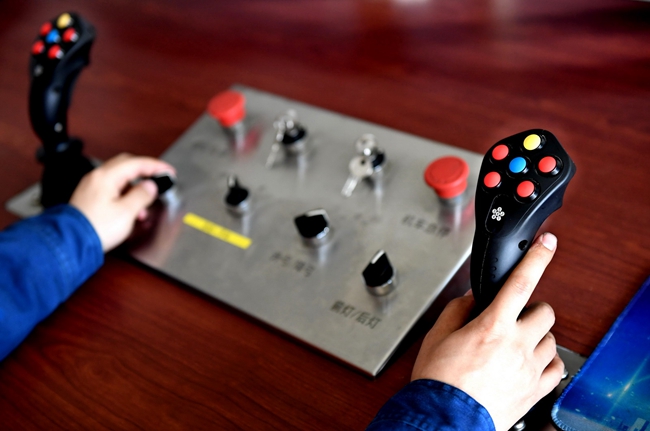
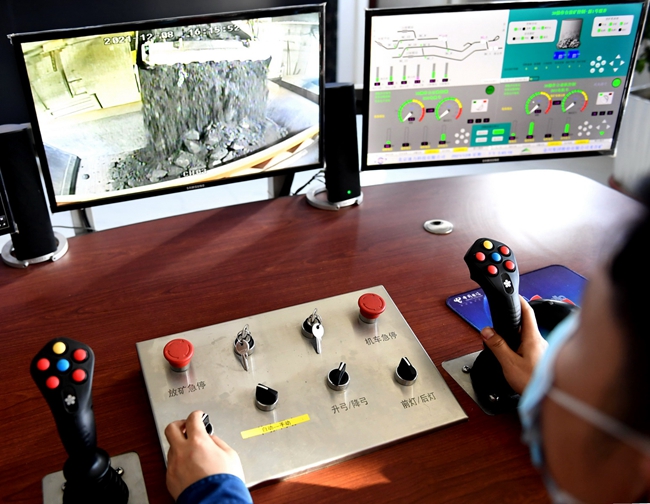
近年來,金川集團公司5G+智能工業(yè)項目的升級改造,徹底改變了傳統(tǒng)作業(yè)方式,崗位職工勞動強度持續(xù)降低,安全管控和現(xiàn)場文明生產(chǎn)水平有力提升,職工作業(yè)環(huán)境有效改善。
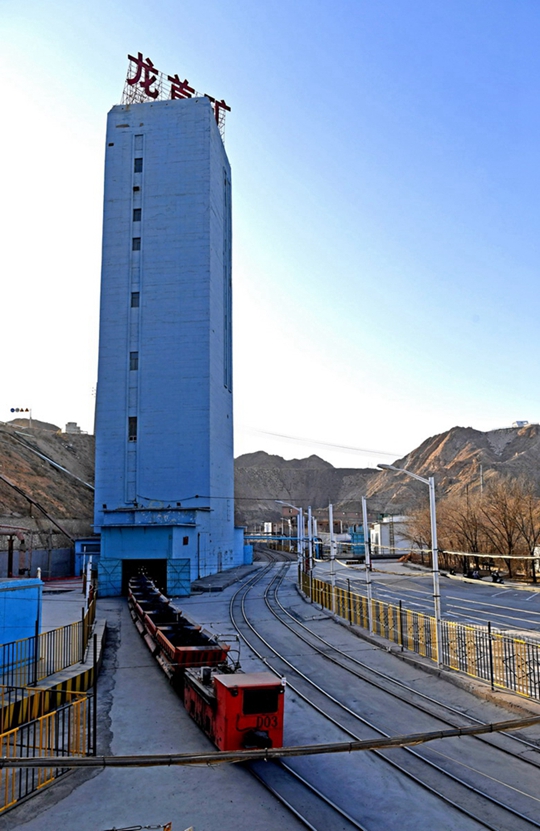
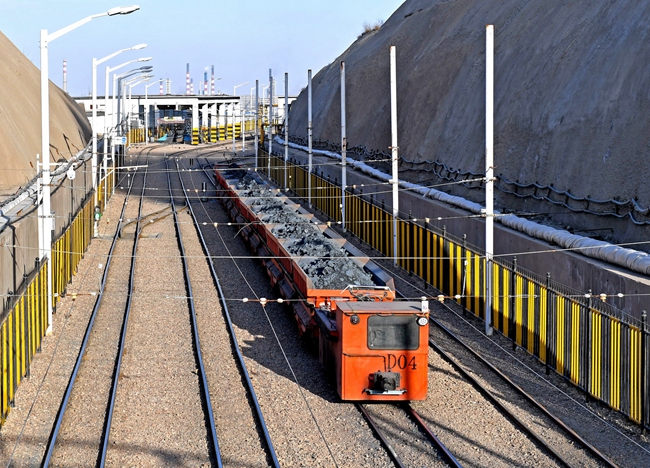
龍首礦有軌運輸電機車正通過5G無線通信網(wǎng)絡進行無人駕駛運行。
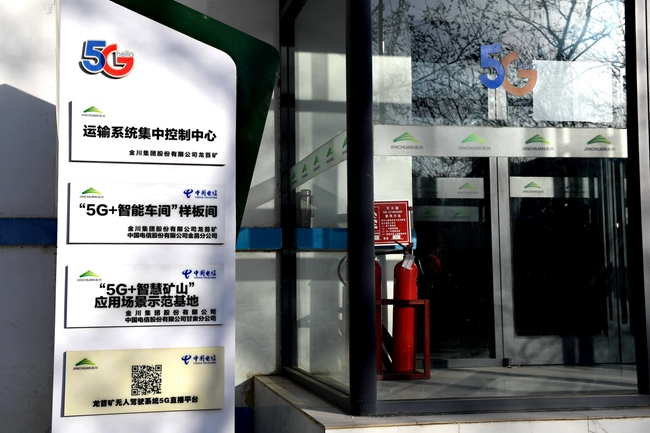
5G+智能化系統(tǒng)不僅在千米井下,還在全國最大的電解鎳智能化成品包裝生產(chǎn)線上發(fā)揮作用。
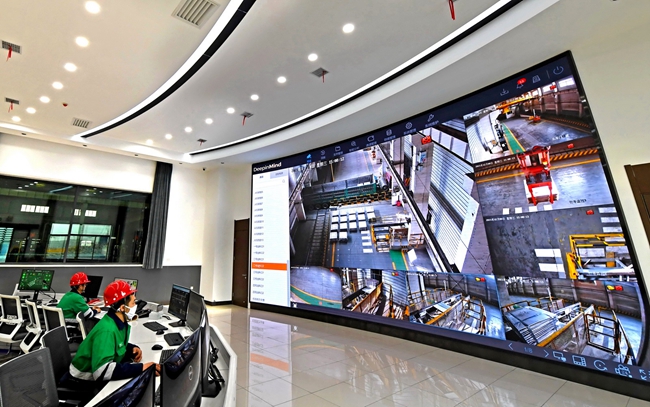
走進大板鎳智慧車間運營管控中心,室內(nèi)偌大的環(huán)形曲面屏幕上,顯示著高清的現(xiàn)場生產(chǎn)畫面,讓觀者猶如身臨其境;窗外碼垛機器人、無人叉車卻在忙碌地剪切、整形、噴碼、包扎……
“我們只需在電腦前監(jiān)測和看護就行?!辨囈睙拸S成品車間副主任白翔介紹,成品車間是鎳產(chǎn)業(yè)鏈最后一道工序,抬板剪切、打包噴碼繞膜、掛吊整形等作業(yè)需要30人完成,勞動強度大,作業(yè)效率較低,每天作業(yè)量只有80噸至110噸。
“以前,這個工序是純手工生產(chǎn)線,智能化改造后的作業(yè)量是以前的3倍多”白翔說。
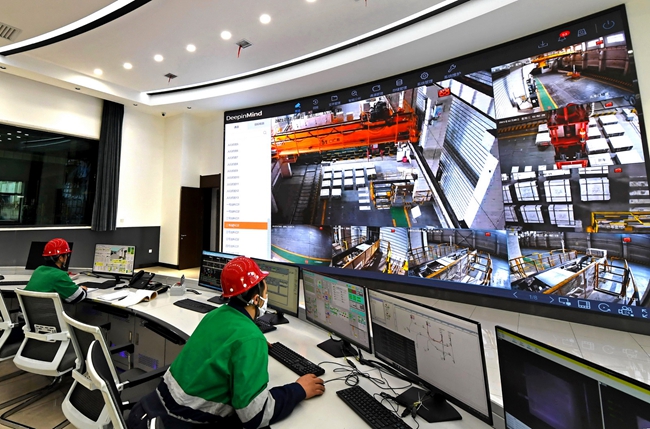
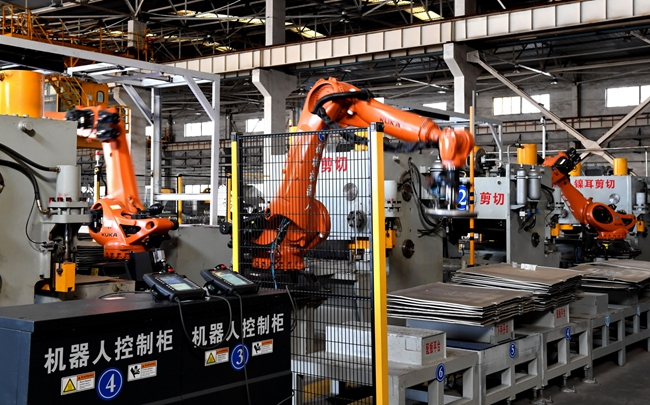
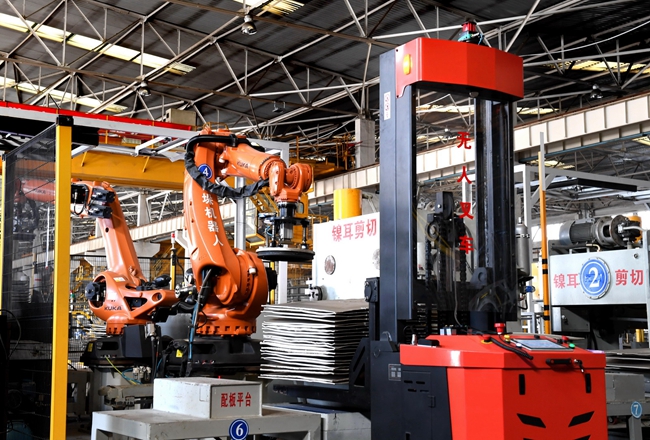
鎳冶煉廠對大板鎳加工包裝生產(chǎn)線進行智能化改造,實現(xiàn)全流程自動化,數(shù)據(jù)集成、信息在線檢測監(jiān)控,5G+工業(yè)互聯(lián)網(wǎng)等新一代信息技術與傳統(tǒng)產(chǎn)業(yè)深度融合,持續(xù)提高勞動生產(chǎn)率。
金川集團公司緊跟科技進步步伐,充分利用5G+工業(yè)互聯(lián)網(wǎng)、人工智能等先進科學技術,推動產(chǎn)業(yè)高端化、智能化、綠色化發(fā)展。(新甘肅·甘肅日報記者 高 檣)